A new lease of life for your Gutmann.
Cut running costs and upgrade to the latest wheel technology. It's an investment that quickly pays off.
A SMART INVESTMENT
Blast wheel upgrades offer exceptional returns on investment. A straight swap to next-generation blast wheel technology can unlock significant savings on parts, abrasive and energy, while delivering more uptime, more consistent quality and a more stable process. All this without the disruption or the capital outlay of buying a new machine.
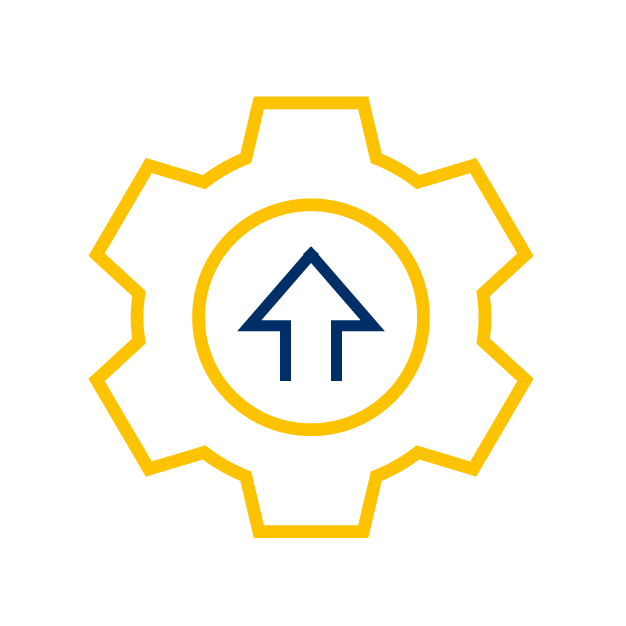
WHY UPGRADE?
Gutmann blast machines are equipped with blast wheels that are no longer state-of-the-art. Depending on the exact wheel type, they come with one or more features that keep your running costs higher than they need to be. Much higher.
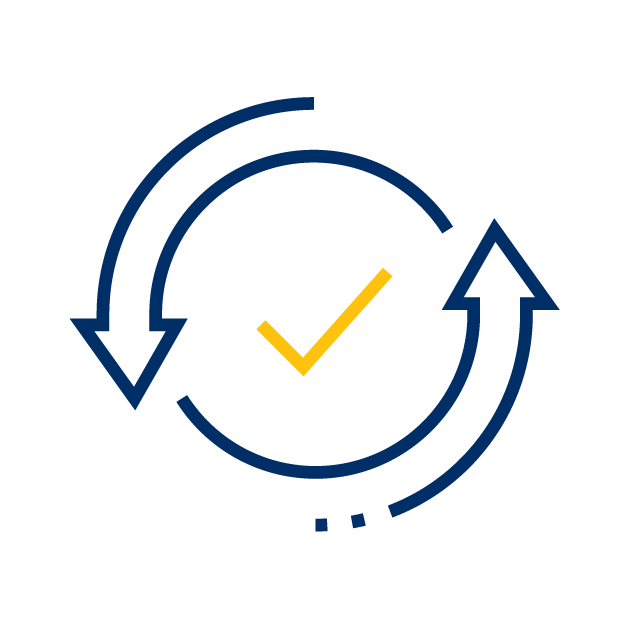
WHY TITAN?
TITAN blast wheels represent the very latest in blast wheel technology. Continuously improved and made from hardened tool steel, they are designed for maximum uptime, radical ease of maintenance and exceptional blast results.
GUTMANN |
TITAN 15 Tool Steel | Benefits | |
Wear parts & material |
Belt drive & single disc wheel Cast Iron or steel |
Direct drive & double disc wheel Hardened tool steel (blast wheel housing in Manganese steel) |
Noise reduction as no belts Less wear and tear |
Blade Lifetime | 300 hours | Up to 2,500 hours | Up to 700% lifetime improvement |
Maintenance & Efficiency |
More maintenance due to replacement of belt bearings. Inefficient belt drives leads to more maintenance. Single disc wheel causes discharge of blast media
|
Lower maintenance with direct drive i.e. no belt and bearings Better blast efficiency Double disc wheel for better blast media control and more effective blasting process. |
50% reduction in time spend on maintenance. 20% lower energy cost from eliminating energy loss in belt drive. Superior blast results Less wear of blast media |
Cost & ROI |
Annual operating cost 27k for 1 machine with 4 blast wheels.
|
One off investment for 4 blast wheels Reduced annual operating costs €18k |
€9k annual cost savings 4-year payback under ideal conditions (operating 8 hours a day) |
You’ve kept your Gutmann shot blast machine going. That’s great! But you’re running on technology that is at least 20 years out of date.
Instead of buying replacement wheel parts at increasing cost, upgrade to new blast wheels and benefit from a leap in performance and a considerable drop in running cost.
TOOL STEEL WEAR PARTS
TITAN wear parts last up to six times longer than Gutmann parts, dramatically increasing maintenance intervals.
Due to its clever design, maintenance access is easy, halving the time it takes to exchange parts.
DIRECT DRIVE
TITAN’s direct drive saves energy - up to 20%* compared to V-belt driven Gutmann wheels.
It also doesn’t need the Gutmann wheel’s energy-intensive abrasive pre-acceleration, resulting in further savings.
*20% electricity savings average
DOUBLE DISC WHEEL
TITAN’s double-disc design keeps abrasive on course and on target.
Gutmann wheels are single-disc and therefore prone to abrasive drifting out of the core assembly, causing wear and diluting blast results.
Ready for your upgrade?
Say goodbye to outdated blast wheel tech and hello to new performance and lower running costs. Get in touch to find out how much you can gain and save.
- Improve quality
- Increase efficiency
- Reduce downtime
- Simplify maintenance
We are where you are - across Europe, North America, India, and China. We supply equipment, spare parts and support quickly and expertly.