Wheelbrator's range of airblast cabinets extends from manual to highly automated machines.
All dry and free running abrasives can be used. And there is a choice of suction and pressure fed and wet blast cabinets for production specific applications.
The advanced features of these machines ensure an efficient process and maximum operator comfort. They are robustly built and specifically designed in a compact form to aid space saving in enclosed environments.
In the wet blasting process a water-abrasive mixture is used. The water washes contaminants like grease and oil away, and dust is eradicated. Wet blasting is often used for refurbishing parts such as motor and compressor parts, or in very clean environments, such as aerospace and medical applications.
Pressure Fed Air Blasting
The pressure fed air blast cabinets from Wheelabrator have been designed specifically for production applications where a high work output is required, combined with optimum abrasive quality.
Suction Fed Air Blasting
Suction fed air blast cabinets have been designed specifically for production applications where a less aggressive surface treatment is required. Suction fed blasting has a lower performance than pressure fed blasting, but uses significantly less compressed air.
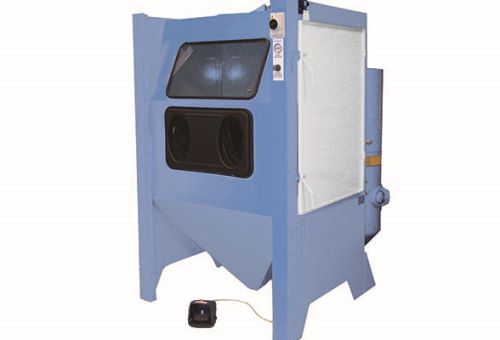
Technology:
Airblast
Application:
Cosmetic Finishing
SmartLine Airblast Cabinet
Mild steel constructed, standard, suction and pressure fed airblast cabinets to ensure efficient operation and maximum operator comfort in full production environments.
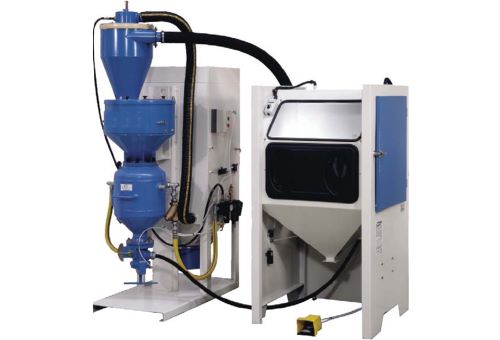
Technology:
Airblast
Application:
Cosmetic Finishing
Vacu-Blast Ventus Airblast Cabinet
A favorite in the Aerospace and medical industries, where keeping abrasive quality is very important, the Ventus range is versatile enough to allow all types of personalization. Available as pressure fed or suction fed cabinets.
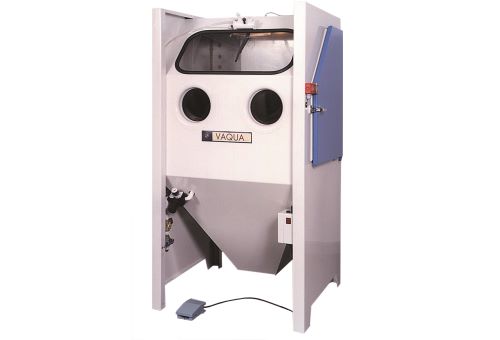
Technology:
Airblast
Application:
Cosmetic Finishing
Vaqua Wetblast Cabinet
The Vaqua range has been designed specifically for production applications where a high work output and optimum performance is required. The Wet Blast process provides component cleaning, degreasing and finishing in one operation.